|
|
|
|
NAPOPC.CAN DA Server Version 2.1 Release:
Support I-7565-H1, I-7565-H2, and provide Virtual CAN interface for programming. |
|
|
|
|
|
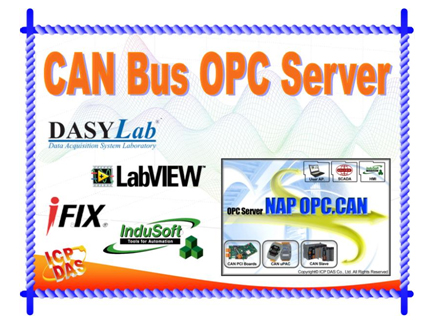 |
|
|
|
|
|
Nowadays, more and more CAN-based devices are introduced in accordance with the keen demands from automotive and industrial fields. There is no a common hardware driver for current various OS is always a headache to all system developers. Therefore, OPC server became a good solution to turn the disadvantage over. Here the new updated version NAPOPC.CAN DA Server 2.1 formally released by ICP DAS is a CAN OPC server to be as an expert bridge between ICP DAS CAN products and third party software for OPC client, provides the easy-to-use user¡¦s interface for developers to access CAN ports by different APIs. Version 2.1 supports the full range of CAN products from ICP DAS, include Ethernet, RS-232, USB, PCI bus and PCI Express bus hardware interfaces. Under the software architecture, users¡¦ applications are even able to access these CAN products via virtual CAN drivers directly without the OPC clients. The software application architecture is shown below. |
|
|
|
|
|
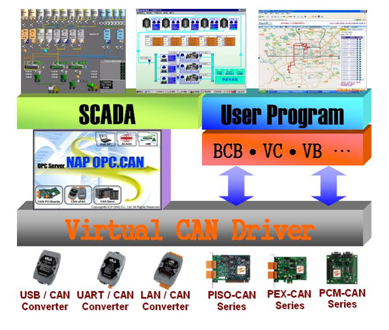 |
|
|
After applying the Virtual CAN Driver, an integrated library, all of the CAN products connected with the PC will be regarded as the virtual CAN bus ports of the PC. The Virtual CAN Driver can scan all of the CAN ports and give each searched port a unique sequence No. which is a virtual CAN port No.. Users only need to know the mapping table of the CAN devices and virtual CAN ports No which can be accessed by the APIs of the Virtual CAN Driver. No matter what kinds of the hardware interfaces the CAN products have, each application can apply the same APIs to access the CAN network. Therefore, it is helpful to develop the control system with different CAN products, or to transfer the hardware interface of the applications.
For more detail, please refer to the user¡¦s manual in the following website:
http://ftp.icpdas.com/pub/cd/fieldbus_cd/can/virtual_can/ |
|
|
|
|
|
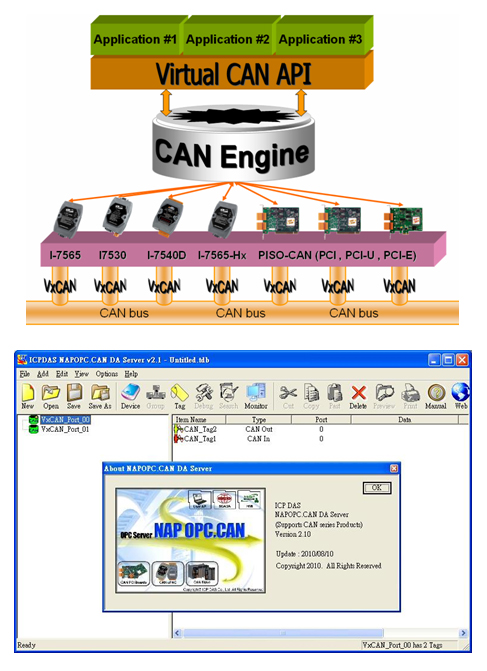 |
|
|
|
|
|
Features: |
|
|
- OS environment: Windows 2000 / XP
- Follow OPC 1.0, OPC 2.0 Data Access Standards
- Configure CAN baud rate with OPC utility
- Configure CAN hardware filter by the APIs of the Virtual CAN Driver
- Provide CAN Engine Utility to monitor the CAN messages.
- Collect the data from the different CAN devices in one OPC server.
- Provide the CAN devices and the virtual CAN port No. mapping table.
- Load previous configuration or scan all CAN devices manually while the Virtual CAN Driver boots up.
- Provide the APIs of the Virtual CAN Driver
- VC6 / C#.NET / VB.NET Demos for the APIs of the Virtual CAN Driver
|
|
|
|
|
|
Support Product List: |
|
|
|
|
|
|
|
|
NAPOPC.CAN DA Server and manual can be download from:
http://www.icpdas.com/products/Remote_IO/can_bus/can_opc_server.htm
The following website is for CAN bus total solution of ICP DAS, it provides more information about the CAN devices supported by OPC server.
http://www.icpdas.com/products/Remote_IO/can_bus/can_intro.htm |
|
|
|
|
|
|
 |
back |
|
|
|
|